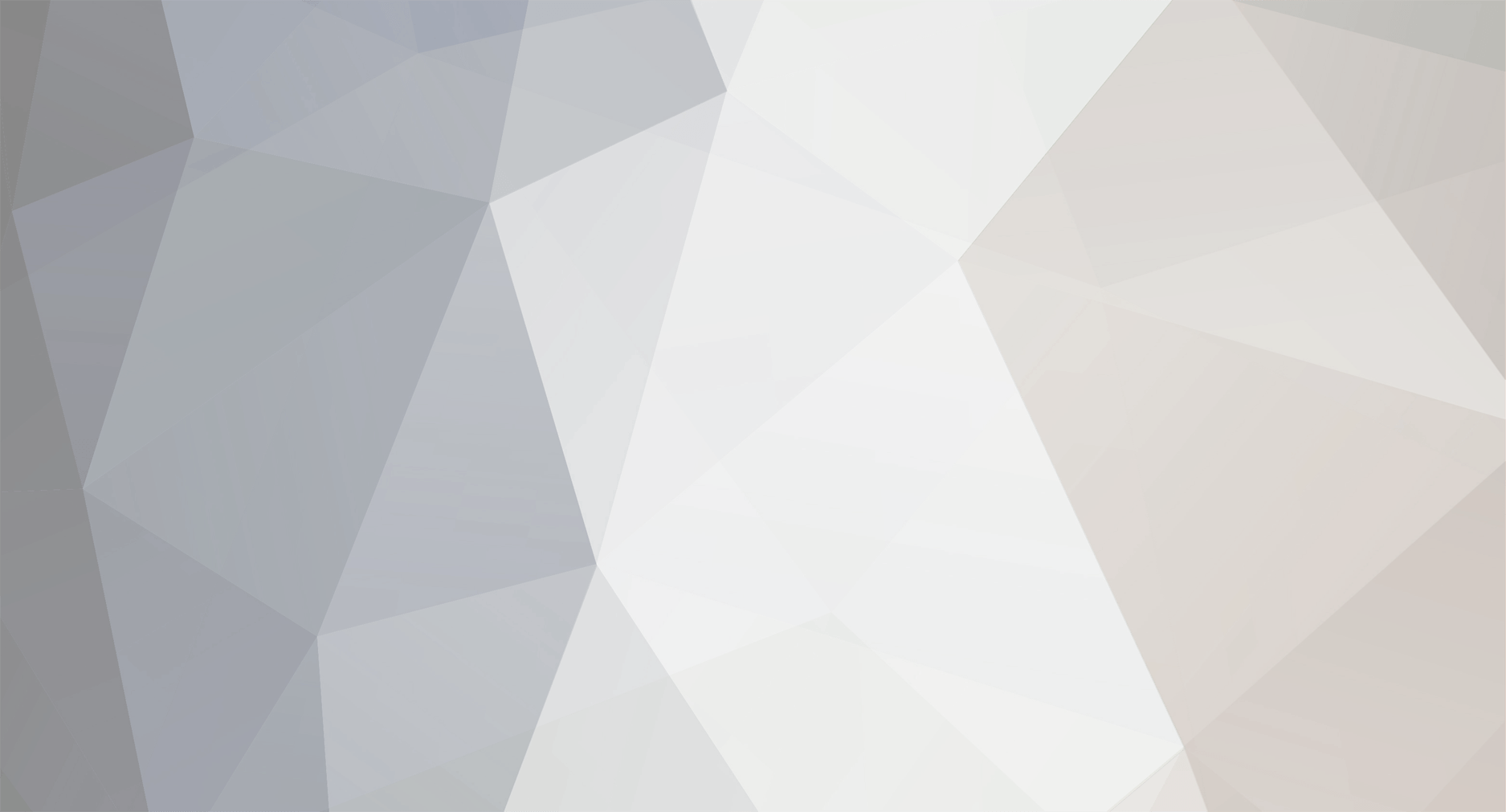
vince3004
Membres-
Compteur de contenus
193 -
Inscription
-
Dernière visite
Type de contenu
Forums
Blogs
Boutique
Calendrier
Téléchargements
Galerie
Articles Auto
Sites
Annuaire Auto
Petites annonces
Tout ce qui a été posté par vince3004
-
Pour tout savoir sur le NOS
vince3004 a posté un sujet dans Induction Forcée. de .::Club TRD Quebec::.
Le protoxyde d’azote (Nitrous Oxyde) à l’état gazeux est utilisé dans le domaine automobile afin de rendre une voiture plus performante. Le symbol chimique du protoxyde d’azote est N2O. Ainsi, chaque molécule de protoxyde d’azote est donc composé chimiquement de deux molécules d’azote et une molécule d’oxygène. D’autres applications se servent du protoxyde d’azote notamment dans le domaine médical. Parfois le protoxyde d’azote est incorrectement appelé NOS qui est en fait l’acronyme de la plus grande compagnie qui fabrique des systèmes d’injection de protoxyde d’azote (Nitrous Oxide Systems). L’injection de protoxyde d’azote dans la chambre de combustion d’un moteur à combustion interne afin d’augmenter la puissance du moteur à été découvert au début de la seconde guerre mondiale par l’industrie de l’aviation Allemande . Des milliers d’avions Allemand étaient équipés du fameux système‘GM-1’ qui ajoutait du protoxyde d’azote dans l’entrée d’air afin de compenser pour la faible densité d’air à haute altitude ainsi que la faible quantité d’oxygène. L’armée britannique royal a aussi utilisé les systèmes de protoxyde d’azote dans ses avions. Par contre, l’armée de l’air américaine n’utilisait pas ce système sauf dans un cadre expérimental. Il est important de se demander, si le protoxyde d’azote est si dangereux pour la fiabilité d’un moteur, pourquoi tant d’avions ont utilisé ce système ? Dans ce pays, durant les années 1950, le fameux coureur de stock car Smokey Yunick à découvert les bénéfices du protoxyde d’azote afin de gagner des courses jusqu’à ce que NASCAR découvre ce système et en interdise l’usage dans les courses. Vers la fin des années 70 début des années 80 le protoxyde d’azote à été redécouvert par les amateurs de course en ligne droite (drag) pour ses nombreux bénéfices. De nos jours le protoxyde d’azote, comme plusieurs autres modifications tel les camshafts plus agressifs, de plus gros carburateurs, les ratios de compression élevés, de meilleurs systèmes d’entrée d’air ainsi que d’échappement, est un moyen d’ajouter plus de performance à votre moteur. Et … comme toutes les autres modifications… peut-être même plus car il est très facile d’en faire un mauvais usage… il peut ainsi y avoir un prix à payer au niveau de la fiabilité et de la durabilité. Le protoxyde d’azote et un gaz incolore et ininflammable. Le protoxyde d’azote à un léger goût et odeur sucré. Il est non-toxique, non-irritant et quand inhalé en petite dose rend euphorique d’ou le nom gaz hilarant. Lorsque inhalé sous forme pure et en grande dose il peut mener à la mort par asphyxions car à la pression atmosphérique ambiante, l’oxygène dans le protoxyde d’azote n’est pas disponible au corps. Une propriété du protoxyde d’azote est qu’à environ 565 degrés F., il se divise en azote et en oxygène respectivement. Lors de son injection dans l’entrée d’un moteur à combustion interne, il est aspiré dans la chambre de combustion et, durant la phase de compression, lorsque l’air atteint la température de 565 degrés F. un mélange à haute teneur en oxygène en résulte. Si nous ajoutons plus de carburant durant l’injection de protoxyde d’azote, l’effet est tout aussi impressionnant sinon plus qu’une augmentation du ratio de compression d’un moteur. Les systèmes d’injection de protoxyde d’azote pour automobile sont utilisés pour une courte durée de performance enivrante. Le protoxyde d’azote a cet effet car il possède un plus haut taux d’oxygène que dans l’air disponible dans l’atmosphère. Le protoxyde d’azote a 36% d’oxygène versus 23% dans l’atmosphère. De plus, le protoxyde d’azote est 50% plus dense que l’air dans l’atmosphère à la même pression. Ainsi, 1 pied cube de protoxyde d’azote contient 2.3 fois plus d’oxygène qu’un pied cube d’air. En faisant rapidement vos mathématiques dans votre tête vous vous rendrez compte que si nous substituons une quantité d’air par du protoxyde d’azote dans un moteur en ajoutant la quantité approprié de carburant, le moteur va produire plus de puissance. Simple constat, le protoxyde d’azote est semblable à un supercharger ou une augmentation de la compression dans le sens ou, durant la phase de combustion, il augmente dramatiquement la pression dans les cylindres du moteur. Ainsi, lorsque nous augmentons signification la pression dans les cylindres du moteur nous augmentons aussi la tendance du moteur à détonner plus rapidement. C’est pourquoi presque tous les moteurs équipés de système d’injection de protoxyde d’azote nécessite un délais additionnel (retarder l’ignition) lors de l’injection du protoxyde d’azote. L’augmentation de la pression dans les cylindres cause aussi, lorsque mal utilisé ou mal installé, des problèmes avec les seals de tête de gaskets ou des défauts dans les pistons ainsi que d’autres problèmes. Je dois ajouter que peut importe la méthode de faire subir des détonations plus importantes à un moteur, comme un trop haut niveau de pression de la part d’un turbo/supercharger, un niveau trop bas d’octane dans un moteur à haute compression ou un niveau trop haut de compression vont aussi causer ce genre de problèmes. Un autre problème avec le protoxyde d’azote est d’en obtenir facilement partout et d’avoir la bonne quantité de carburant lors de l’utilisation (notons que les pompe à essence venant avec l’auto de base sont conçue pour une voiture non modifiée). Si vous fournissez du protoxyde d’azote à votre moteur sans la bonne quantité de carburant, le mélange air/protoxyde d’azote au mélange de carburant va rendre le problème de détonation encore pire. La température dans la chambre de combustion va augmenter en flèche et des problèmes importants sont certains d’arriver. Si la proportion est au point ou trop de carburant est envoyé, les avantages du protoxyde d’azote vont diminuer rapidement. Comme vous pouvez le voir, le protoxyde d’azote est comme n’importe quel modification visant l’amélioration des performances dans ce sens, lorsque utilisé intelligemment et installé de façon professionnelle, fonctionne très bien. Toutefois, lorsqu’il est mal utilisé ou mal installé, le protoxyde d’azote peut diminuer la fiabilité et la durabilité de votre moteur. Des petites doses de protoxyde d’azote peuvent être utilisés pour obtenir 25-35% plus de puissance. Selon mon opinion, plus de protoxyde d’azote que ça dans un moteur non modifié (forgé/sleever/renforcé) compromet trop la fiabilité et la durabilité d’un moteur. Prenez un moteur 82 ou 84, augmentez la puissance à 300hp et ne faites rien pour augmenter la durabilité et votre moteur va éventuellement souffrir. Lorsque vous passez le cap des 35% en ajout de performance avec du protoxyde d’azote vous devez regarder pour forger vos pistons, mettre des meilleurs connecting rods, mettre des meilleurs bearings, etc. Le protoxyde d’azote est aussi une très bonne valeur par dollar investit par unité lorsque installé correctement. Le côté plus désagréable par contre est que le plaisir ne dure pas longtemps. L’augmentation de la puissance dure aussi longtemps qu’il reste de protoxyde d’azote dans la bouteille. La moyenne des bouteilles est d’environ 20 livres et avec un moteur V8 cela peut se traduire en une utilisation continue de 20 secondes de protoxyde d’azote. Donc le protoxyde d’azote n’est pas si mauvais que ça lorsque bien installé ! Il peut être intéressant mais à mon avis ne remplace pas un système turbo ou supercharge. Traduction par: Jean-Philippe Béique Source: http://fr.wikipedia.org/wiki/Azote Source2: http://www.idavette.net/hib/nitrous.htm -
4afe?
vince3004 a répondu à un(e) sujet de thebutcher dans Moteur/Transmission/Entretien. de .::Club TRD Quebec::.
En général ce sont des piece qu'on peu avoir au dealer avec le numero de piece ou bien ce sont des piece compatible avec ceux qui sont sur l'auto^^ Toyota a un programe de code de piece internationale, surtout pour les piece moteur Mon ami a un 20v blacktop, et il a pu commander sa timming belt chez toyota! -
-
-
Je met ça dans les suggestion... parce que je vous suggere d'aller la Ce gars la est un spécialiste de la performance toyota et jdm. Surtout pour les mr2, c'est lui le king des mr2 au québec. J'ai vu plusieurs job qu'il a fait et ses clients que je connais on tojours été satisfait de ses service . Alors si vous avez des trouble ou bien des projets avec vos toy, allez le voir ;) Mecanique G.T. 3208 Boul. Frontenac Ouest, Thedford Mines, Qc, G6H 2C4 (418) 423-4136 Modo; déplacer ce post au besoin merci
-
4afe?
vince3004 a répondu à un(e) sujet de thebutcher dans Moteur/Transmission/Entretien. de .::Club TRD Quebec::.
bin la... les piece de 4age ça coure pas tant les rue que ça!!! Quand je vais dans les courre a scrap c'est TRES rare de voir un bluetop pi encore + rare de voir un redtop... Pi le 4agze... si vous en trouver un dites moi le svp Perso, je te dirai dy aller avec un 20v silvertop, tu achetes le moteur et tu vas voir quelqu'un qui a déja swapé 20v(CP Performance ou Mécanique GT) pour t'aider avec la couete de fil, pi ça fitte dans les meme support avec les mêmes cardans. Je te conseille le prendre le moteur avec la tranny, parce qu'elle sera gearé plus cour que celle de ton 4afe... anyway celle du 4afe dois être aussi usé que le moteur !!! Quand tu à toute les bonnes pieces, ça peu prendre une journé et c'est fait Puis tu t'en tire en bas de 1200$ si tu fais tout toi meme, c'est plutôt intéressant -
Convertion brake disc pour Tercel/Paseo
vince3004 a posté un sujet dans Les "How-To's". de .::Club TRD Quebec::.
Source originale http://board.tercelonline.com/viewthread.php?tid=19163 Starlet GT EP82 / EP91 rear disc brake conversion for Tercel/Paseo HOW-TO (56K ye be warned) I spent all winter hoarding performance goodies for the Terc. I finally had one free day and awsome weather so I decided to start modding -sly- I took lots of pics so here's a DIY Qball style... --------------------------------------------------------------------------------------------------------------------------------------------- Before you start. Put the transmission in 1st gear if it's Manual. Make sure it's in "park" if it's an automatic. I had my Terc on 4 jackstands so I did none of that. Jack up the back of the car using the factory lift points on the rocker panels and then place jack-stands under the rear axle. Now remove the wheel. Let's get down to business. This is the little nasty rusty drum brake setup Toyota equiped our Tercels with. Although completly adequate for the weight of the vehicle, it just looks plain fugly when you've got some sweet alloys on your ride. Start by removing the dust cover using a flat-head screwdriver/chisel and a hammer. Tap the cap alternating sides to pop it off. Now you'll see the cotterpin and nut retainer. Remove the pin using a set of needle-nose pliers to straighten the pin legs and then pull it out. The nut retainer should come right off after the pin has been removed. Now remove the nut with a 22mm socket. Both sides of the car use regular thread. No reverse threads here. So "righty-tighty, lefty-loosy" applies here too. Remove the washer. The bearing should now come out easily. After the bearing has been removed the drum should come off. There may be some hesitation. If you need better leverage, try putting the wheel back on with a couple of lugnuts and use it for leverage. There is also an adjuster inside the drum brake assembly that can be accessed through a hole in the backing plate which is plugged with a rubber grommet. Release the shoes like that if you just can't get the drum off otherwise. Older drums usually have lips worn into the drum which makes them harder to remove. This is what you should be looking at after removing the drum. Remove the giant retractor spring by prying it off with a screwdriver or do like I did and use your hands. It's really not all that stiff. It's function is to retract the brake shoes when you let off the brake pedal. Next you need to remove the retaining pins. These hold the brake shoes in place. There's one in each shoe. Reach around back with one hand and hold the pin in place. Then with the other hand, push the front washer in and twist to release the washer. Now remove the pin, spring and both washers. You should be able to remove the shoes one at a time. Remember not to lose the bottom spring that connects the two shoes. Now remove the e-brake cable. Just pull the spring back with your hand and slip the cable out of the bracket. Release the e-brake cable from the backing plate by removing the two little bolts with a 10mm socket. Now it's time to get under the car and unbolt the solid brake line from the axle. A standard open-end wrench will most likely strip the nut so use a linewrench. This is a special wrench that has more contact surface than an open ended wrench which will protect the nut and allow you to loosen even the most stubborn nut. It's like a box-ended wrench with a slot in it to slip over the pipe. Now unbolt the backing plate from the axle by removing the 4 bolts with a 14mm socket. It's now time to prep the Starlet GT disc rotors. I know it's really rusty but I love it Remove the old inner bearing seal with this wicked seal puller. That seal puller looks like a weapon you say? Well I'd have to agree:mad: After pulling the old seal. The bearing comes right out. Let's hit the parts washer for some cleanup. You can tell I love this part....mmm....solvent -lol- Clean the bearing out well and then blow it out with compressed air. You want to get ALL the old grease out. Do the same for the rotor. So fresh and so clean-lean-lean...sorry....anyways - back at the ranch... Repack the bearings with wheel bearing grease. I do it manually but you can use a bearing packer. You can use either the Tercel or Starlet bearings. But I prefer to use the Starlet bearings since the race is installed in the rotor already. Make sure to put some grease in the cavity of the rotor too to make sure the bearings will always have grease. Now it's time to re-install a new Genuine Toyota Japanese built inner bearing seal. Again the USDM/CDM 91-99 Tercel seals fit the Starlet GT rotors. I didn't get a pic of the seal driver I used so here's what it looks like on top of the old drums. Use it to pound the new seal in nice and straight. Apply some wheel grease to inside of the seal to protect it later during sintallation. Now that the rotors are preped it's time to go back to the axle. Clean off the flat mating surface with a wire brush and sand paper. Then cover it with anti-cease just in case you ever need to remove it in the future. Bolt on the new backing plate with the longer bolts from the starlet GT setup. The Tercel bolts are too short. Coat the spindel with some more axle/wheel grease to protect the seal during installation. Slide the rotor onto the spindel and re-install the newly re-packed outter bearing, washer, nut, nut retainer, cotter pin, and dust cap. All those parts can be used from either your Tercel or the Starlet. They are all interchangable. Bolt the caliper bracket to the backing plate. 12mm wrench. Now's also a good time to clean the rotors off with some aerosol brake cleaner to get all the grease and solvent off before installing new pads. Open up one of your boxes of brand new Genuine Toyota pads. -sly- Install the pad shims. Again..rusty I know.-love- Use some anti-squeek and apply it to the contact patch of the shims. Time to prep the caliper. I had already rebuilt these but I had a couple of pieces left. Copper washers for the flexible brake hose. Make sure to retract and rotate the piston into this position before bolting the caliper to the bracket. The little bumps/tabs on the brake pads have to fit into that slot in the piston to keep it from rotating. So make sure it's installed properly. Now snap the other end of the hose in place on the bracket with the C-pin. Attach the hard line from the Starlet setup. The Tercel line doesn't fit. You may be able to bend it to fit but if you have the Starlet lines, use them. IF you don't want to wreck your Tercel setup, then go out and buy some hard lines with connectors and bend it to suit your needs. They cost less than $10 each. :censored: that's sexy. Ok when you're done admiring your own work it's time to get messy again. Time to hook up the Starlet GT e-brake cables. I won't sugar coat it. This part suxorz.-blah- You have to remove the aluminum exhaust heat shield to get at the e-brake cables. You're gonna have to make some room to work in there so unhook the rear muffler hanger and slide the whole exhaust off to either side. Then using a large drilbit to drill out the 3 aluminum rivets that hold the shield in place. Don't worry. You can re-install it later. Now get in the car and take your 10mm socket, extenssion and ratchet with you. Loosen the adjustor nut as far as you can without backing it off the bolt all together. Get back under the car and remove the cables with a 10mm socket. Now you'll run into a problem. At least I did on my 98 Tercel. Starlet cable on the left - Tercel cable on the right. I had to fab up some sleeves out of a piece of 10mm conduit to solve the problem. MINT!!!! Unfortunatly the Starlet is a little shorter than a Tercel so it's cables too are a little shorter than the Tercel's. So you can only use one mounting point on each side. Route the cable through the stock location on the axle. You will have to remove the grommet and then pass the cable through the hole. Reinstall the grommet over the cable and squeeze it back into the hole. I didn't get any pins to attach the cables to the rear calipers so I had to make some. I used some TOYOTA bolts that I had lying around. I cut them to length and drilled them for a cotter pin. Now that you're done with the cables you can re-install the heat shields using some standard aluminum pop-rivets. Go back into the cab and tighten that e-brake tentioner nut. That's it. You're done. Now just bleed the brakes and top off the brake fluid. Put the wheels back on and you're ready for a test run. BTW this setup will fit with 13" stock wheels. Good luck guys -ccolguy- -
LSD: the basic
vince3004 a répondu à un(e) sujet de vince3004 dans Suspension/Tenue De Route/Freinage/Pneus. de .::Club TRD Quebec::.
-
Turbocompression; Pour apprendre
vince3004 a répondu à un(e) sujet de vince3004 dans Induction Forcée. de .::Club TRD Quebec::.
Bon, avec les étapes suivante, un 3SGTE 2ndgen pourrais avoir dans les alentour de 300hp. Si vous voulez plus vous devrez upgradé le turbo, ou bien changer carréement de style de turbo. L'upgrade de turbo permet d'aller chercher quelque gain supplémentaire mais tout en étant limité au housing stock du turbo autant coté exhaust que coté compresseur. Un quasi bolt on serais de changer pour le compresseur du ct26 de supra tout en gardant le exhaust housing du CT26 du 3SGTE, cela permeterais daller chercher qque hp jusquau redline. Un premier upgrade pour le CT26 serais de mettre un compresseur plus gros. Ex: To4e trim 45-48-50-54-57- 60-1 etc.... avec celui ci pas de perte de hp au dela de 5500rpm (cest le cas du CT26 dorigine sur 3SGTE) et moins de challeur (plus fiable!) et pourra aller au dela du 16-17psi que je metterais max sur un CT26 stock. Un 25 psi serais possible si on a un bon intercooler a la disposition. Un désavantage est que plus gros compresseur = plus lourd. donc spool un peu moins vite, moi mon 54trim spool 200rpm plus tard. cest tout.le top end en vaux la peine. souvent le monde font faire un rebuild du turbo en meme temps. Le clipping serais quelque chose a considéré selon ce que vous cherchez comme courbe de puissance. Plus le clipping est accentué en degré, plus le lag est gros, mais plus fort sera le boost. Un autre aspect pour ceux qui cherche un gros top end power vont changer la turbine pour une plus grosse. ainsi le hot side du turbo doit etre remachiné pour laisser la place a la nouvelle turbine. encore une fois, plus la turbine est grosse, plus le lag est gros, plus fort est le boost. les turbo avec turbines en ceramique ne peuvent pas etre clippé (ps turbine en ceramique est plus leger donc enleve du lag). Enfin l'option du dual ballbearing aide beaucoup a réduire le lag, vraiment beaucoup. mais assez dispendieux, a la place de toute investir sur un CT26 aussi bien s'acheter un garrett GTxxR Ou bien un nouveau style de turbo est a considéré. Il y en a des quantité phémenal, des kits complet, partiel, custom etc... les Garretts sont reconnu pour leur durabilité. Et la serie Ball bearing GT R est tres bien et completement. http://www.atpturbo.com en ont une panoblie qui répondrons a vos besoins les plus fou, du 350hp au 2000hp. tout cela dépendra de votre portefeuille ;) Ceux ci vous amenerez a un autre dilem. Wastegate interne ou externe. tout cela dépend de votre sérieux dans votre projet. La wastegate interne necessite moins de budget mais créé de la turbulance dans toute lexhaust, cest quelque hp et un peu de lag. La wastegate exhaust est une bonne alternative. Celle ci doit avoir un exhaust manifold avec un port de wastegate externe. Malgré quelles soient plus efficace que les waste gate interne, ceux ci la plus pars du temps coupe 90degré carré la ou les 4 se rejoints, ou encore pire pres de la sortie d'un seul cylindre. Lideal cest davoir un port qui va suivre le mieux possible le flow sans le changé brusquement de direction. Un des moteur de course de Toyota a bénéficier de l'ingenieuse idée de mettre le port a meme le hot side du turbo, donnant une ligne continue pour le flow avec une legerement déviation de maximum 15degré.beaucoup mieux que les 90degré des setup a vendre majoritairement. Haschel si tu voix ca peux tu posté la photo du moteur de Toyota a la fin de la section Exhaust manifold du livre de corky bell? thanks ;) D'autre informations pour vous bientot! -Oly -
Turbocompression; Pour apprendre
vince3004 a répondu à un(e) sujet de vince3004 dans Induction Forcée. de .::Club TRD Quebec::.
Bon, comme jai dit l'ennemie numéro #1 dun moteur est la détonation, et le premier moyen de l'évité est d'avoir un bon ration Gas/Air. La vous roulez trop riche, vous perderez de la puissance et votre consommation de gas sera gargantuesque. Pour le contraire, si vous roulez trop pauvre (lean) sa va marcher, mais la température du moteur va monté dramatiquement et amener a la surchauffe du moteur et ensuite a la détonation. les pires scénarios sont des pistons et connecting rods défoncés, des gaskets de tetes fini. Un bon moyen de savoir si vous roulez trop riche ou trop lean, c'est un A/F meter qui se branche sur la sonde a oxygene (O2 sensor). Un EGT (Exhaust gas temperature) peux aussi aider a la lecture, si la temperature est trop haute, vous roulez lean, mais celui ci est plus viable lorsque le moteur est chaud) Ces lectures vont permetterons de voir si votre mixture de gas est dite ''stacïometrique'' ou pas. ceci étant dit, si vous mixture est encore riche, vous pouvez monté le boost jusqua temps pour vous ayez atteind un niveau acceptable. si au contraire vous runnez lean, il est temps de modifié de systeme de gas pour en fournir plus et cest a partir d'ici que sa commence a couter vraiment cher sans meme avoir ouvert le moteur. Un petit ajustement de monté la pression de gas en montant le voltage a celle ci peux donner un peu plus de gas, mais ce moyen est tres limité. Et dans ce qui suis, rien de va pas sans l'autre. Les injecteurs doivent etre remplacés, pour de plus puissant, la fuel rail doit etre shimmé ou bien carrément remplacé par une autre. Le pompe a gas aussi est a changé pour une a plus haut débit. le meilleur choix pour la pompe est la pompe 255lph (litres per hours) de walbro qui coute moins de 100$USD. Un fuel pressure regular est aussi demandé pour baissé la pression du gas. C'est l'ECU du moteur qui gere les injecteurs, et ils doit savoir comment injecté de gas celon le boost et controllé le timing. Celui d'origine ne fait pas la job rendu a plus de tant de psi (vari celon le moteur, 12psi pour le 3SGTE 2eme generation). Plusieur option s'offre a vous je vous enumere les principales et les meilleurs. Un upgrade d'ordinateur peux etre fait, mais sont tres couteur, on parle de 1000$ souvent. La compagnie modifira electroniquement l'ECU pour amener son fuel et timing map pour +/- 6 psi de plus. Ils metterons un timing plus aggresif et enleverons fuel cut, cut off de RPG et vitesse. C'est un upgrade simple (Plug and play) mais bon juste pour un type de setup: le votre car vous devez dire au techniciens quel sont vos modifications actuel. un autre option est un ordinateur piggy back. celui ci modifira les entrée et sortie des signaux de l'ordinateur d'origine pour ajuster quelque PSI de plus au timing et fuel map. Le greddy E-manage et le Apexi s-AFC sont de bon exemples et font bien le job. ceux ci tourne environ dans les 300-400$ La derniere options, la plus couteuse est l'ordinateur completement ''stand-alone'' tels que le AEM, Autronic, SMT, SDS EFI, Megasquirt, etc...) Ceci permet d'enlever completement l'ordinateur d'origine et permet d'avoir une mixture parfaitement stacïometrique cest a dire 14.7 molecules d'air pour une de gas. (14.7:1). Cette mixture est bonne dans un moteur N/A (naturely Aspirated), dans le cas dun moteur turbo, le map s'ajuste comme ceci: Quand est le turbo n'est pas embarqué, on peux leané la mixture jusqua 17:1 des fois, mais lorsque le turbo embarque sa doit runné plus riche , 12.5:1 est la mixture ideal au point de vu safety/power Un wide band o2 sensor peux etre une necessité pour ajusté parfaitement le systeme étant donné que le o2 sensor d'origine est plus ou moins precis. Les systeme Stand alone comme ceux ci coute cher mais en faut la peine, ils vous permettent d'aller chercher de precieux HP, tout en étant tres sécuritaire et vous permet de remodifié les donnés si vous remodifiez votre bloc moteur par la suite. on parle de 1000$ en montant pour la plus pars des cas. Le systeme Megasquirt lui nest vraiment pas cher (350$ USD environ ) mais est un systeme DIY (do it yourself) pour ceux qui aime tout faire eux meme comme moi et exige un portable pour programmé l'unité mais on a pas besoin de le garder dans l'auto. (www.megasquirt.info) C'est la parti la plus cruciale d'un bon setup. Un systeme avec les meilleur intercooler du monde peux brisé si la mixture n'est pas bonne. Donc un bon tuning est important. Un bon timing également est vital, afin d'évité les backfire (Un char qui fait des flammes en arriere sa veux pas dire necessairement qui marche: c'est peux etre qu'il est mal timé!) le taux d'octane est crucial aussi, le setup turbo ne doit jamais au grand jamais rouler en bas du 91 D'octane. l'octane est un anti détonnation, plus il y a d'octane, plus la combustion ce fait rapidement. Petro Canada vendent a certaine stations de l'octane 94. oubliez l'octane booster vendu chez cacan tire, sa ne faux rien. Ils marque augmente jusqua 7 points, mais ce n'est que 0.7 D'octane. Ils va vous en falloir en maudit pour passé de 91 a 100 d'octane des ptite cacan a 15$!!! Le toluene qu'on retrouve dans ces cannettes est disponible dans les shop de peinture pour moindre cout, au dire, 10% de toluene dans la tank de gas fait passé le 92 d'octane a pas loin de 96 taux d'octane. tres bon! Vous voulez plus de jus encore? prochaine étapes a suivre!!! -
Turbocompression; Pour apprendre
vince3004 a répondu à un(e) sujet de vince3004 dans Induction Forcée. de .::Club TRD Quebec::.
Bon, vous voulez plus de jus? c'est ici que ca commence a couter cher.... Le changement d'un intercooler serais tres bien. D'origine ceux ci sont souvent mal placé, tres petit, mauvais efficacité et a un tres mauvais flow pouvant entrainé de la détonation. l'ennemie #1 d'un moteur turbocompressé est la détonation. Pour évité celle ci, il y a 2 moyen principale. Voici le premier (je parlerais de la 2e dans l'étape de la modification du systeme EFI) Baissé l'air de la temperature d'entrée du moteur est tres important, c'est pourquoi un intercooler demande un choix judicieux pouvant saufer la vie de votre bloc moteur. Plus l'air qui rentre dans le moteur est froide, plus cest sécuritaire, et plus le moteur va développé de la puissance. (FMIC) l'option 1 est de mettre un intercooler plus gros avec un bon flow en avant du radiateur, ceci donnant un look tres extravagant. Tres efficace a haute vitesse, celui ci donne malheureusement un peu de ''lag'' au turbo. Il y en a plein a vendre sur ebay ou autres commerce. un bon intercooler frontmount peux couter 400-600$ et un kit avec piping peux couter jusqua 1000$. (W/A IC)L'option 2 est un intercooler refroidit a l'eau, attention pas avec l'eau/prestone du moteur!!! un échangeur de chaleur doit etre placé en avant du radiateur, avec un pompe electrique a bon débit et une tank de surplus (pour y mettre de la glace encore mieux pour la drag), Lavantage est la réponse, étant refroidit a l'eau (l'eau dissipe jusqua 10X mieux la challeur sur l'aluminium que l'air peux le faire!). mais est moins efficace a grande vitesse que le frontmount. Ceci coute plus cher effectivement et est plus lourd. donc si vous vous misez pour aller manger des V8 sur l'autoroute, le frontmount est conseillé, si vous preferez faire des bon 0-100, le water to air (refroidir a l'eau) est recommandé. ces modifications pourrais vous donner un 10-30 supplémentaire celon le type d'intercooler, épaisseur, etc.... et en meme temps votre setup sera encore plus fiable! Plusieur personne font des spray d'eau sur l'intercooler refroidir a l'air, sa peux aider un peu! et certain utilise meme du CO2 qui viens completement gelé l'intercooler! Alors, ce n'est pas assez puissant? continuez a la prochaine étapes a venir! -
Turbocompression; Pour apprendre
vince3004 a répondu à un(e) sujet de vince3004 dans Induction Forcée. de .::Club TRD Quebec::.
Bon, maintenant que votre moteur respire bien, vous etes moins a risques. La prochaine étape serais de monté la pression du turbo. Ceci se fesant avec un Boost controller. Plusieur type on été inventés. Les manuel ball and springs, les valves bleeders, et les EVC (eletronic valves controller). Les Ball and spring sont muni d'un ressort et d'une bille a linterieur de la valves, vous l'ajuster avec une visse et celui ci ne laissera passer le signal a la wastegate tant qu'il naura pas attein la pression demandé. Ceci créé un boost plus long a atteindre mais plus direct. Facilement trouvable sur ebay. Les valves bleeders eux produise un boost plus progressif mais instentanément. Ce trouve également sur ebay et meme dans les shop de pneumatic pour quelque dollars. Les electronic valve controller sont beaucoup plus dispendieux, il suffit de tappé EVC sur ebay pour qu'il vous en trouve. Ceci fonctionne avec l'unité de commander situé dans l'auto, et de solenoid pres du turbo qui controlle le signal alland a la wastegate. Attention, avant de faire monté le boost, je vous sugere un Boost gauge, et de savoir les limites respectables que votre ordinateur et systeme dalimentation en gas est capable de fournir. Exemple sur un 3SGTE, l'ordinateur coupe a 12psi et le systeme de gas est bon jusqua 15-16psi mais le fuel et timing map est bon jusqua 12psi, apres ils envois autant de gas qu'il peux. Un fuel cut defencer est demander pour enlever le fuel cut a 12psi. Ceci varie d'un moteur a lautre de la maniere d'enlever ce fuel cut. D'origine la plus pars des moteur (toyota en particulier) la pression du turbo est a 7-8psi. Passé de 7psi a 12psi ayant suivant létape #1 que jai recommandé vous permettera daller vers un 20-25hp supplémentaire, naturellement sela varira sera la taille du turbo, mais étant donné que les turbo d'origine cest petit, cest pas mal ceci que sa donne. Monté le boost a 15-16psi vous irez chercher un total suprenant de 50hp environ. un 3SGTE de 2e generation avec ces modification developpera pas loin de 300hp apres cest 2 étapes @16psi. Vous voulez plus de jus encore??? passez a l'étape #3! -
Turbocompression; Pour apprendre
vince3004 a posté un sujet dans Induction Forcée. de .::Club TRD Quebec::.
Écris par OlyST185 Bon cest la question que beaucoup de monde se pose, lorsque jai un turbo, que dois-je upgradé pour aller chercher de la puisse. En effet le turbo possede la qualité de pouvoir aller chercher de tres bon gains en puissance comparativement au moteur N/A (naturally aspirated). On entend souvent dire que c'est fragile un moteur turbo, Ce n'est pas vrai, c'est si c'est mal monté que c'est fragile. Dans tout les moteurs turbocompressé d'origines, sans exceptions, la ligne d'exhaust est beaucoup trop respectif. Ci les manifacturiés aurais mit une ligne qui respire mieux, ils auraient eux beaucoup plus d'avantage dont plus de puissance et au point de vue de la fiabilité. Une ligne d'exhaust d'origine est tres souvent tres restrictive donc vous empeche de monté le boost car vous aurez trop de ''backpressure'' dans votre systeme d'echappement, ceci pouvant causé des bris de turbo, ou des gaskets/seals/rings dans les chambres de combustion. La turbo demande beaucoup a un moteur c'est pour ca qu'il doit bien respiré. Alors inutile de vous dire que le premiere chose a faire avant de monté le pression du turbo est d'avoir une ligne d'exhaust moins restrictives et une entrée d'air également moins resctrictive. Vous pouvez videz vous catalyseurs et installer un bon filtre a air (Apexi, K&N sont les 2 meilleurs, évitez le HKS, blitz et autres marques comme Ractive). Avec un bon filtre a air, un gain de 10-15hp est prouvé sur le dyno. Vider le catalyseur aide de quelque peu mais souvent insufisant et pas bon pour l'environnement. Vous remarquez un leger gain en puissance et le turbo embarquement plus tot. Une ligne d'exhaust de 2pouces et demi ou 3pouce est a considéré. 2pouce et demi vous gardera une bonne puissance a bas régime, mais un haut régime assez limité jusqua un certain point. le 3pouce va vous enlever un peu de puissance a bas régime mais vous donne une tres grande marge de puissance a haut régime et est meme bon jusqua 600hp alors que 2 1/2 est bon jusqua 350-400 si le setup est bien monté. En gros, moins la ligne est restrictive, mieux c'est. Attention, ce n'est pas le cas de l'exhaust manifold que je vais parler plus tard. De ce fait, une legerement augmentation du boost se produira ainsi et une bonne difference a la puissance du moteur sera appercu, certain disent que c'est l'amelioration la plus bénéfique a une setup turbocompressé. Juste en laissant le moteur respiré mieux comme ceci, beaucoup de monde serons entierement satisfait de la performance de leur bolide. dans le cas d'un 3SGTE un parle d'un gain total de pas loin de 30-40 hp et beaucoup de torque. Mais comme le boost en addictive... on en a jamais assez! a suivre dans le step 2! -
Supercharger A-Z
vince3004 a répondu à un(e) sujet de vince3004 dans Induction Forcée. de .::Club TRD Quebec::.
The Twin Screw Supercharger The twin screw supercharger at first glance appears to look similar to a roots supercharger both inside and out. The two technologies are indeed similar, however there are significant differences. At the heart of the twin-screw supercharger are two rotors, or "screws" that rotate towards each other. The rotors mesh together and draw air from the back of the supercharger. The twisting rotors move the air to the front of the supercharger, while compressing the air before discharging through a port at or near the front of the supercharger. Because the compression is done inside the supercharger, this design produces less heat than a roots supercharger - in fact, it is almost as thermally efficient as a centrifugal design. Like the roots design, the twin-screw is a fixed displacement supercharger (meaning that it pumps a fixed volume of air per revolution), and because the tolerances between the rotating screws are very tight, its ability to create boost at low rpms is unparalleled. These characteristics make it ideal for trucks and towing vehicles, where low to mid range power is primary in importance. Another important advantage of the twin screw compressor is its reliability. Unlike a roots supercharger, the rotors in a twin screw supercharger do not actually touch, so there are virtually no wearing parts. For this reason, twin screw compressors are commonly used to pressurize cabins in passenger aircraft. Like roots superchargers, twin screw superchargers are self lubricated and do not tap into the engine's oil supply. One disadvantage of the twin screw design is that, because it has an internal compression ratio, the twin screw is compressing air even when it is not sending boost to the engine (i.e. under cruising or deceleration). An internal bypass valve releases the pressurized air, but because it takes work to pressurize the air in the first place, the twin screw supercharger draws more power from the engine than while not under boost. Like the roots, the throttle body must be placed before the compressor because it is a fixed displacement supercharger. The Centrifugal Supercharger Although the centrifugal supercharger is founded on a technology much newer than either the roots or the twin screw, it was the first supercharger to be successfully applied to automotive applications. Unlike the roots, the centrifugal supercharger is NOT a positive displacement / fixed displacement supercharger because it does not move a fixed volume of air per revolution. The centrifugal supercharger essentially operates like a high speed fan propeller / impeller, sucking air into the center of the supercharger and pushing it to the outside of the rapidly spinning (40,000 + rpm) impeller blades. The air naturally travels to the outside of the blades because of its centrifugal force created by its rotating inertia. At the outside of the blades, a "scroll" is waiting to catch the air molecules. Just before entering the scroll, the air molecules are forced to travel through a venturi, which creates the internal compression. As the air travels around the scroll, the diameter of the scroll increases, which slows the velocity of the air, but further increases its pressure. The centrifugal supercharger enjoys several advantageous characteristics that make it the most popular supercharger design in the aftermarket world. First, it is simple and reliable because it has very few moving parts - just a few gears and the impeller. Second, the centrifugal supercharger produces very little heat because of its internal compression ratio. It is also small in size and very versatile because it can "free-wheel" and allow the engine to suck air through it or even flow air backwards. For this reason it can be placed anywhere in the intake tract - it can even "blow through" the throttle body, meaning it can be mounted nearly anywhere. It is also the most thermally efficient supercharger, meaning that it produces the lowest discharge temperature. The only significant disadvantage of the centrifugal supercharger is that it must be spinning at a relatively high speed before it begins to make a significant amount of boost. For this reason, it is not helpful in creating boost (and power) at low engine rpms. Normally the supercharger only begins to create boost at around 3000 rpm, and the boost curve gradually and increasingly rises with engine RPM. Many centrifugal superchargers do not have a self-lubricating oil system, and draw oil from the engine's oil supply. The disadvantage to this is that you must tap the oil pan for the oil return line. However, in doing so, the supercharger becomes virtually maintenance free. Some manufacturers make a "self-contained" centrifugal supercharger that is self-lubricated like roots and twin screw superchargers. The Turbocharger You may be wondering where the turbocharger fits in to this equation. Technically, a turbocharger IS a type of supercharger - one that is driven by exhaust gasses rather than from a pulley that draws power from the engine's crank. Because the turbocharger relies on a technology substantially different from the three traditional supercharger technologies discussed above, it is beyond the scope of this article. That's it for part 2 of the series - next time we'll pull everything together and discuss what goes into making a complete supercharger system, and how the supercharger works in conjunction with the engine. The Air Intake System Because a supercharged engine draws substantially more air than a normally aspirated engine, it is important to minimize intake restrictions. To ensure a smooth delivery of air to the supercharger, most supercharger systems include a high-flow air filter as well as low-restriction tubing or ducting to deliver air from the atmosphere to the supercharger. It is important to maintain a clean air filter to minimize the particles that come into contact with the supercharger's impeller, rotors, or screws. Most supercharger systems will draw air from behind the fender wall, where there is an abundance of cool air that has not been heated by the engine. Because superchargers heat air as it is compressed, a cool air supply helps to keep the charge temperatures at a reasonable level. On a non-intercooled application, the cold air pickup can lower the charge temperature by up to 60 degrees! On most vehicles the incoming air charge passes through a Mass Air Flow sensor (aka MAF) on its way to the supercharger, although on centrifugal superchargers, the Mass Air Flow sensor can be mounted after the supercharger ("blow-through" setup). The Mass Air Flow sensor measures, you guessed it, the mass of air that the engine is drawing. This reading allows your engine's ECU (Electronic Control Unit) to calibrate and deliver the appropriate amount of fuel for the incoming air charge. Once the supercharger has worked its magic, the air must be delivered from the supercharger to the engine intake. Although many roots and twin screw superchargers bolt directly to the manifold, most centrifugal superchargers require an extra tube called a Discharge Tube to carry the air to the intake through the throttle body. This tube will normally be mandrel bent to minimize restrictions. The Bypass Valve Compressor surge is a problem that affects most superchargers and develops when the supercharger is creating boost, but the throttle shaft is closed. Although not a problem on some low-boost (5psi or less) applications This condition can occur under deceleration or while shifting between gears, and can cause the car to sputter and chirp. Under surge, the compressor forces air into the closed throttle body until the pressure inside the throttle body is higher than the amount of pressure being created by the supercharger, and the air tries to pop backward through the supercharger. At that point, pressure is released inside the throttle body and the compressor forces air back through the supercharger and into the throttle body, which again has nowhere to go, and the process repeats. While surge normally is not highly damaging to the engine it is certainly annoying and can cause damage with time. To eliminate these problems under surge conditions, a bypass valve (sometimes called an anti-surge valve) is used to release the excess pressure. The bypass valve is actuated using intake manifold vaccuum, which opens the vent valve and releases pressure in the air-intake. Air is either released into the atmoshpere (blowoff valve) or recirculated back through the supercharger compressor (bypass valve). The Intercooler / Aftercooler Some supercharger systems include an aftercooler (more commonly called an "intercooler"). The purpose of the intercooler is to remove heat from the air to create a cooler, more densely packed air charge Vortech Style. Although the intercooler is not necessary on most street applications, its performance becomes increasingly important on higher-output systems (with correspondingly higher charge temperatures). The intercooler can be compared to a automotive radiator, only instead of cooling water or coolant, the intercooler cools the air. Air-to-air intercoolers force the air through a large air-cooled finned and fluted core, normally mounted in front of the car's radiator. Air-to-water intercoolers force the incoming air charge through a much smaller finned and fluted heat exchanger that is cooled by water. The water is, in turn, cooled by a compact radiator that mounts next to the stock radiator. The two main purposes of the intercooler are 1. to allow more boost on a given octane level of fuel without detonation, and 2. to help create more power by condensing the air charge. Thus, intercoolers are very common on high boost applications (10+ psi) and on roots-style superchargers, where discharge temperatures are higher than normal. Most street supercharger systems (5-8psi) do not come standard with intercoolers. The Fuel System As increased amounts of air are pumped into the engine with the supercharger, so too must increased amounts of fuel be delivered. This is where the power gains come from. Most stock fuel systems are not up to the task of delivering the increased volumes of fuel demanded by a supercharged engine. Without a proper fuel system, your engine may run lean, detonate, and obviously perform below its potential. Because every engine is different, the fuel system requirements vary greatly with different vehicles and with different supecharger systems. Sometimes larger fuel injectors and a larger fuel pump is required. On some applications, a fuel management unit (FMU) will do the job by restricting the fuel return line to build up fuel pressure. On other applications, additional fuel injectors are mounted to the intake manifold, while on some applciations the stock fuel system works like a charm. Fortunately most supercharger systems include all of the fuel system components necessary to tune the engine to perfection. On some race kits, tuner kits, custom installations, and high output systems, it is up to the engine tuner to determine the engine's fuel requirements and tune the fuel system accordingly. The Ignition System The engine's ignition system serves the important role of telling the spark plugs when to fire so the compressed air and fuel is ignited at the exact right time to produce maximum power. Ignition timing can be advanced, causing the spark to fire earlier, or retarded, causing the spark to fire later. Ignition timing is critical not only for performance reasons, but also for engine longevity as it used to eliminate detonation (aka spark knock). With the added air and fuel that is compressed in a supercharged engine, the engine is closer to its detonation threshold. To avoid detonation, many supercharger systems retard the ignition timing, thus reducing maximum cylinder pressures and temperatures, and moving away from the detonation threshold. Because retarding the ignition timing causes a slight loss in power, a higher octane fuel or an intercooler are recommended for optimal performance, both of which allow for more timing without detonation. To ensure a complete and cool burn, high quality, cool heat range irridium spark plugs are also recommended for use on supercharged engines. The Pulley All superchargers are driven by a pulley that sits inline with the accessory belt or crank pulley. The size of the supercharger pulley is what regulates the speed at which the supercharger spins. Obviously, a smaller pulley turns the supercharger faster, and vice versa. The pulley is easy to change on all superchargers and is often used to increase (or decrease) the ouput of the supercharger. A simple pulley-swap can equate to huge power gains if the rest of the system is up to the task (in particular the fuel and ignition system). The Rest Other components serve self explanatory roles. Mounting brackets obviosly are used to attach the supercharger to the engine in a position such that the pulley can be spun from the accessory belt or an additional supercharger belt. The belt tensioner keeps the belt tight around the supercharger pulley, which is important to avoid slippage, especially on centrifugal superchargers which spin at high RPMs. Hardware, hoses, and fittings are of course necessary to attach the supercharger to the engine, connect the oil and fuel lines, and to install the ignition components. That rounds out the complete supercharger system. Remember that every supercharger system is designed to meet the specific needs of the engine, given the desired level of output from the supercharger. For this reason, some supercharger systems come with only a few of the components mentioned in this article, while others come with it all. Generally speaking, higher output supercharger systems come with more components to meet the increased volume of air, which is why they cost more than entry level systems. Congratulations if you made it through all three parts of this series - you deserve a gold star and are now a supercharger expert! -
Par Jim Moody: Superchargers A-Z This article lays down the foundation of how superchargers came into being by taking a look at the fundamentals of creating more power, and looking back in history at where and how the technology originated. Making More Power - Four Possibilities with One Common Thread When it comes to extracting more power from an engine, the common goal, simply stated, is to burn more air and fuel per time. There are essentially four ways to achieve this end. 1.) The first way to make more power, is to make the engine more efficient by tuning the air and fuel delivery, reducing intake and exhaust restrictions, reducing rotating mass, enhancing spark energy, and tuning engine timing. This is the purpose of most aftermarket modifications, like air filters, ignition programmers, exhaust systems, etc. These modifications are very popular because they provide added power, they look good, and they sound good. Moreover, they can be done piece by piece, so your car can build with your budget. The problem with these kinds of modifications is that performance gains are small - often negligble and unnoticable. This is because most engines today are tuned fairly well from the factory, and are not equipped with highly restrictive intake or exhaust components, which would reduce fuel economy. In other words, if you're looking for more moderate power gains, you'll need to get to the heart of the engine where power is really made. Most of these modifications essentially have one goal in mind - make the engine more efficient so it can burn more air and fuel in a given amount of time. 2.) You can also make more power by speeding up the engine, i.e. spinning it at a higher RPM. This technique is very effective in producing more horsepower while keeping the engine lightweight and small. If you look at some of the fastest race cars in the world, you will find them spinning at incredibly high RPMs. The only drawback is that to spin at such high RPMs requires very high quality (and expensive) engine parts that can withstand the torture from the rapid rotation. Furthermore, the increased RPM substantially increases wear and tear on the engine resulting in decreased reliability and shorter engine life. Most street cars and trucks have a redline RPM of around 4000 to 7000 RPM. Spinning the engine faster than the redline RPM in street vehicles is risky without extensive engine modifications to support the higher rotational speeds. The goal with this option is also to burn more air and fuel per time. 3.) Another obvious way to make more power is to simply use a larger engine. Bigger engines burn more air and fuel, and hence, make more power per revolution. Of course, if it were that simple, we'd all be driving around with V-12s. You can fairly easily increase the size of the engine's displacement by boring the cylinders and running a larger piston, or by lengthing the stroke of the crank, but you can only go so far before you've bored the entire cylinder away or your piston is slamming into the cylinder head. To go really big requires a bigger engine, probably with more cylinders. The drawbacks of a bigger engine include their increased size (duh!?), increased weight, and reduced fuel efficiency. In addition, using a larger engine normally is not practical because it would require an entire engine replacement, which would be prohibitively expensive, and would require extensive modifications to mount it to the vehicle. Again, though, the goal of this technique is to (yep you guessed it) help the engine burn more air and fuel per time. 4.) The final way to make more power is to pack more air and fuel into the combustion chamber before igniting it. The end result is the same as using a larger engine. The problem with this technique is that it's not as simple as telling your engine to suck more air and fuel - it's restricted by atmospheric pressure. At sea level, atmospheric pressure is 14.7 psi, which is a measure of how densely packed our atmosphere is with air molecules. As elevation rises, air thins which, as you probably noticed on your last skiing / snowboarding trip, robs power from the engine. Now imagine if you could trick mother nature by making atmospheric pressure 21psi. You'd be packing around 50% more air, which means you could burn 50% more fuel, meaning you'd be making approximately 50% more power. You've probably already figured out that this is exactly what a supercharger does - it compresses air to pressures above atmospheric pressure (boost), thus packing more air into the engine. And you've probably also figured out that the goal of this technique is to burn more air and fuel per time. By utilizing this technique, a small engine can act like a big engine. It is more efficient because it has less weight and rotating mass. In addition, because you can control when the compressor (supercharger) is sending compressed air (boost) to the engine, and when it is not, you can enjoy stock fuel efficiency when the supercharger is not sending boost to the engine (normally at half throttle or less). In reality there are more than four ways to make more power, but these are the four most conventional ways. You can also use a more potent fuel source that has more potential energy. This is the idea behind Nitrous Oxide and other high-energy fuels - a topic beyond the scope of this article. A Brief History of the Supercharger You may be wondering, "Who first thought of compressing air before sending it to the combusion chamber?" Don't run to the library just yet. We'll tell you! It seems that just before the turn of the century (1900 that is), a German engineer named Gottlieb Daimler (yes, of Daimler Benz, Daimler Chrysler...) obtained a patent for a pump to aid in the delivery of increased amounts of air and fuel to the cylinder, and to aid in the removal of exhast gasses. He didn't call it a "supercharger" in his patent application, but that's what he was describing - this was the birth of the automotive supercharger. But in order to get to the true beginnings, we have to look evern further back in history. Gottlieb's automotive supercharger design was modeled after a twin-rotor industrial "air-mover" invented and patented nearly 40 years earlier by Mr. Francis Roots (from Indiana) back in 1860. This technology is the foundation of the roots type "blowers" still used today! Soon after the roots air movers (they were not called "compressors because they did not compress air - they only moved it) were used in industrial applications, a German engineer named Krigar invented an air pump that itlizied twin rotating shafts that compressed. This technology would go on years later to become the foundation of the Lysholm twin-screw compressor used in today's automotive applications. Apparently our old friend Gottlieb didn't have much luck in the early stages with his new invention, but the idea inspired French engineer Lois Renault, who patented his own type of supercharger soon after the turn of the century. It wasn't long before superchargers started to show up on American race cars. Lee Chadwick is credited with being one of the first American racers to successfully use a centrifugal supercharger in competitive racing, starting in the Vanderbilt Cup in Long Island, New York in 1908. Soon thereafter superchargers took to the air as World War I military engineers looked for new ways to make more powerful airplanes. Because airplanes fly at such high altitudes, the internal combustion engines that worked great on the ground, suffered at altitude in the thinner air. Although the technology wasn't successfully used in combat before the war ended, it was clear that sueprchargers were well on their way to becoming a mainstream power adding device. Meanwhile, back in Germany, Mercedes was hard at work trying to make old Gottlieb's supercharger work. By 1921 they found success and released a glimpse of the first production supercharged vehicle utilizing a roots-type supercharger. Mercedes went on to manufacture several supercharged models with great success in the following years. In the racing scene, supercharged cars were finding more and more success. By 1924, superchargers made their way to the Indy 500. Around the world, racers in Mercedes, Fiats, Bugattis, Alfa Romeos, Buicks, and MGs began using superchargers to help them to the victory circle. Mercedes found great success with their supercharged Grand Prix cars, while Harry Miller's supercharged Indy cars dominated at the Brickyard. In the mid 1930's Robert Paxton McCulloch started McCulloch Engineering Company and began manufacturing superchargers as the first large American commercial supercharger manufacturer. They began developing superchargers for use on American passenger cars and hydroplane boats. This was the start of the supercharger industry in America as we know it today. Then came World War II in 1939, and the Allied forces had an ace up their sleeve in the form of the supercharged Spitfire fighter planes and B-29 SuperFortress bomber. These supercharged planes seemed almost unaffected by the altitude to the delight of Allied pilots and soldiers. After the war, superchargers took on a new life in the world of racing. Alfa Romeo and British Racing Motors used superchargers on their Grand Prix cars to the horror of the competition before they were eventually outlawed. At Indy, there was no such rule, and centrifugal superchargers howled their way to many vicories. By 1950, McCulloch had formed Paxton Engineering as its own entity, which took over the supercharger development and took on the task of creating an inexpensive supercharger fit for use by the general public. After $700,000 in research, and two years of testing, the VS57 supercharger was ready for the public in 1953. Initially it worked only on 1950 - 1953 Fords, but by 1954 kits were made for nearly every commercially available 6 and 8 cylinder engine. The rest is history, as Paxton developed newer and better superchargers until they became a part of life, not only in the world of racing, but also in the street-legal aftermarket world. Today it's hard to keep track of all the supercharger brands and models, but that's the way we like it! The Roots Supercharger (aka "blower") The roots supercharger was originally designed as an air moving device for industrial buildings. The roots supercharger features two counter-rotating lobes that trap air from the intake side of the supercharger (normally at the back of the supercharger), move it around the outside casing of the lobes, and out the bottom of the supercharger through an outlet / discharge port. Like the twin screw supercharger, the roots is a "positive displacement" aka "fixed displacement" supercharger, meaning that it moves a fixed volume of air per rotation. Notwithstanding minor amounts of air-leak at low rpms, the roots supercharger cannot flow backwards like a centrifugal supercharger, and is thus nearly as efficient in its ability to pump air at low rpms as it is at high rpms. What this means is that roots superchargers are very capable of making large amounts of boost even when engine rpms are very low. This makes for great low-end and midrange power, and also makes them great for trucks and towing vehicles. The roots is also self lubricated, and is the simplest of the supercharger designs, meaning it is reasonably priced and very reliable. This is why roots superchargers have been the choice of GM, Ford, Mercedes, and Toyota for OE applications. The only real disadvantage to the roots supercharger is that it creates a lot of heat. There are two reasons for this. First, the roots supercharger does not compress air - it only moves from the intake port to the discharge port (i.e. it is the only supercharger design with no internal compression ratio). All of the compression is done in the intake manifold. Laws of thermodynamics kick in in favor of supercharger designs with an internal compression ratio (centrifugal and twin screw) because they do less work on the incoming air charge. We will leave the mathematics of this phenomenon to a later (much more boring) discussion. Another reason roots superchargers create higher amounts of heat is because they tend to carry some of the compressed air in the intake back into the supercharger because it gets trapped by the rotating lobes that are exposed to the hotter air in the intake manifold.
-
LSD: the basic
vince3004 a répondu à un(e) sujet de vince3004 dans Suspension/Tenue De Route/Freinage/Pneus. de .::Club TRD Quebec::.
Du Club4ag.com: The Normal Differential As we well know, a race car driver wins races from shaving lap times by cornering faster. Because of this many teams and constructors try to make cars that maintain higher cornering speeds. On every car a basic differential is fitted to to distribute the engine's power to the driving wheels. The basic differential gear (d1 below) supplies the power to wheels which is/are loaded with least resistance. This allows the cars wheels to run at different speeds in a turn with least resistance. However, when a car is cornering close to it's limit, the car will exhibit roll, a leaning to one side, causing the inside tires to lose forward traction and lateral grip. The wheels lift and cause excessive spin because of lack of downward force or weight distribution. This wheel spin is useless for acceleration until the tires regain traction and start to translate the power to the ground. An LSD is used to alleviate this wheelspin. Basic Differential Gear system (d1) The Limited Slip Differential Gear An LSD is constructed similarly to the normal differential. (d2 below) (A limited slip differential gear figure d2) As you can see, the pressure plate rings have the side gear, pinion, and the pinion gear locked inside, and behind each pressure rings are a number of clutch plates. When torque is applied to the differential, the differential case will spin and throw the pinion into the pressure ring cam. The pressure ring is then pushed out against the clutch plates thereby squeezing them together. This in turn causes the wheels to gradually lock together, depending on the power applied. This effect limits the wheel spin during hard cornering and applies power to the wheels evenly when more power is applied to the wheels. On acceleration and deceleration, it provides even grip and on neutral power, it frees up for less drag and easier turning. 1-Way, 2-Way, 1.5-Way.......... What Does It Mean? Some manufacturers make LSD's in different configurations and are commonly classified as 1 way, 2way, and 1.5 way. This designation reflects the design of the cam groove which enables the LSD to function differently under different loads. A 1 way differential means that the cam is shaped in such way as to have positive lock only when accelerating. The 2 way is constructed in a way to have positive lock motion in either acceleration or deceleration. The 1.5 way is a new term used to describe the 2 way cam which enables different lock up rates during the two directional forces. The 1.5 distribute positive lock stronger under acceleration than when decelerating. The 1.5 way can provide more forgiving balance when braking than a full 2 way setup, although it is less effective for true racing applications, it provides easier operation for beginners in throttle off conditions. It is also effective for front drive cars which need extra stability during braking. A 2- way limited slip differential - d3 A Comparison of LSD There are many brand and grades of LSD but here's how you rate them. The OEM supplied LSD, standard and optional on many cars today are 2 pinions. This design has very low positive lock and is designed to provide some sporty feel to showroom cars. Because of the nature of this low lock design, it is just slightly more effective than not having one at all. Not a choice for true performance drivers. Barely does doughnuts...! A performance LSD should have at least 4 pinions. This is the design used for racing and rallies around the world. The positive lock ratio and linear lock characteristics is determined by a number of components. The cam profile, clutch plate quantity and size, initial torque of the pre-load spring, as well as the lubricants. Contrary to what manufactures want you to believe, TRD-Toyota Technocraft, Mugen-Honda Racing, RalliArt-Mitsubishi Rally Operations, MazdaSpeed-Mazda, STI-Subaru Technica Int., NISMO- Nissan Motorsports, all have their LSD's made by the same supplier, a Hitachi subsidiary. This is because the majority of the normal differential gears are supplied by them. They use the cheap factory casing and re-work the inside. This limits the size and number of the gears, and clutches thereby sacrificing true potential. They claim 4 pinions but have only 3 or 4 small clutches on one side. They use very high cam profile to put high loads on the clutches so that it can achieve high lock up. The problem with this approach is that the pre-load on the clutches are higher and tires have constant drag. Also, since the clutches are small and few, the load is larger per given surface area, translating into higher operating temperatures and fast wear. Another major disadvantage to this type of LSD has to be the abrupt lock-up, making on-off conditions less predictable and controllable. The true high-quality Limited Slip are supplied by Kaaz and Cusco, who supply majority of racing teams throughout Japan. The Cusco and Kaaz differentials have on the average 10mm oversize clutch diameter and computer stamped oil channels which hold lubricants during operation. The plates number from 6-8 and have very wide selection of pre-load springs to choose from. Since the clutch has to press together less to achieve very high lock-up, the LSD generates less heat and wears much longer. All components are computer ground and shell casing is not stamped as in the OEM and Branded Hitachi units. Over the long run, these units will cost less to operate due to the lower maintenance required in terms of rebuilding and replacement of clutches. Most of all, these LSDs are much more controllable, having a wider, more progressive lock-up and better positive lock up at the limit. They are more streetable because it won't suddenly spin you around in low traction conditions such as rain and snow. You can, but you can also be in control... To add to this, Kaaz differentials have higher quality tolerance levels, represented by computer balanced shell casing and gears, and initial pre-load springs are matched to vehicle applications. The reason for small application list is that they go through 3 years of N1 and Gr. A racing to design the differential design and specifications. I prefer the KAAZ because of cheaper entry price tag too, made even better by introductory pricing in the US markets. Consider it the ultimate in LSD. -
LSD: the basic
vince3004 a posté un sujet dans Suspension/Tenue De Route/Freinage/Pneus. de .::Club TRD Quebec::.
Voici un article intéressant que j'avais trouvé y'a 1 ou 2 ans de ça: In a standard differential, if one wheel loses traction, it will get all the power and will spin, while the wheel with traction gets nothing. The idea of a limited-slip differential is to prevent all power from being applied to only one driving wheel when traction is lost. There are numerous types of limited-slip, positraction, locker, etc. units. The percentage number denotes the percentage of torque applied to the slower turning wheel from the faster turning wheel. In a straight line, both drive wheels turn at the same speed, so no limited slip action is occurring. In a turn, or when one tire is spinning more than the other (such as on snow or ice), with a limited slip differential, 25, 40, or 75 percent of the torque applied to the faster wheel is applied to the slower wheel, effectively 'limiting slip'. A higher lockup percentage will cause increased rear tire wear on the inside tire during cornering -- the tire itself will have to slip slightly to counteract the limited slip's desire to have both tires turning at the same speed. It will also increase oversteer in wet or slippery conditions, but it will also increase understeer in tight corners under dry conditions. This is simply due to the fact that with a limited slip, the drive wheels tend to want to turn at the same speed, making the car tend to want to go in a straight line. When it is slippery, however, both drive tires will tend to lose traction at the same time, increasing oversteer. The advantages are less inside wheelspin when accelerating out of a tight corner. This also translates into more horsepower to the pavement and faster autocross times -- provided that the suspension is tuned for the limited slip. The ability to accelerate out of corners without excess wheel spin can be a great advantage. Om a more technical note: The limited slip percentage (S) is also called the locking factor. It describes the maximum applied torque difference between rear wheels compared with total applied torque. Passenger car LSDs are usually in the 25-40% locking factor range. Limited Slip Locking Factor or Percentage S: (note: drive torque is torque applied to road surface) S = ( Drive Torque Difference Between Rear Wheels / Total Drive Torque of Both Rear Wheels ) x 100% Think of a situation where the two rear wheels are on different surfaces with different coefficients of friction: H = Higher traction, more torque can be applied to road surface L = Lower traction, less torque can be applied to road surface S = (H - L / H + L) x 100% By rearranging the equation a little, you see that for a 25% LSD, the High torque side can be as much as 62.5% of the total while the Low torque side can be as little as 37.5% of the total. 25% LSD Example: H = (( S+1 ) / 2 ) = (( 0.25 + 1 ) / 2 ) = 0.625 L = (( -S + 1 ) / 2 ) = (( -0.25 + 1 ) / 2 ) = 0.375 The H/L ratio, called the bias ratio, is easier for me to think about because it quickly shows how much more torque can be sent to the high side. With a 25% limited slip, it is possible to have 1.67 times as much torque applied to the high side. A 40% LSD works out to a 2.33 bias ratio. 25% LSD Example: H / L = (( S + 1 ) / ( -S + 1 )) = (( 0.25 + 1 ) / ( -0.25 + 1 )) = 1.67 (Bias Ratio) A locked differential has a 100% locking factor (infinite bias ratio) because all torque can be applied to one wheel (e.g. one wheel on ice or in the air). For a limited slip, the initial preload, or break-away torque, allows power application when one drive wheel is on ice or in the air. Open differentials are another story (see snow/ice write-up below). In theory, an open differential has 0% locking factor (1.00 bias ratio) because the torque to each wheel is balanced (H = L). In actual practice, there is some bias because the differential is not friction free. Differentials reduce tire wear and help a car turn more easily by allowing the rear wheels to travel at different speeds while turning corners. The inside wheel must slow down (smaller radius turn) while the outside wheel speeds up an equal amount (larger radius turn). To balance the drive torque at each wheel, more torque is applied to the outside wheel, speeding it up, while less torque is applied to the inside wheel, allowing it to slow down. Open differentials always work well turning. They also apply power very evenly when both rear wheels have adequate traction. However, the big downside, is their torque balancing action when one wheel has much less traction, such as in ice and snow. The torque applied to the wheel with the most traction can only equal the lesser traction wheel. Total applied torque for both wheels is only twice the traction of the worst wheel. Increasing Locking Precentage How do they increase the locking percentage on a diff? Do they just pack more shims in there to make the clutch plates tighter? Or do they re engineer the ramp angles? I have also read that Metric Mechanic adds clutch plates. In this case is the carrier machined to accept more plates? The shim alters pre-load, and too much pre-load provokes understeer. It'd be better to get the locking to almost go away under braking & corner entry, and then come back for power-on exits. The pre-load should be just enough for a smooth transition between the action of the coast & power ramps, and to keep things together when unloaded. But the shim is what people can do. The shim in question is not the 'thrust washer' that the shop manual refers to, but the 'spacer ring' which is shaped like a Belleville spring washer as big as the discs themselves. These are made of stiff spring steel around 2 mm thick. These, as well as the 'dog- eared plates' are selected to shim up the static locking. The torque path has the ramps driving the differential pinion's shaft, and the ramp angle leverages the clamping force applied. Less angle on the ramp offers a mechanical advantage for applying the clutches = more lock. Adding clutches increases surface area for clamping = more lock available. You would have to machine the housing to fit them, so it could weaken it. Hope this is enough! -
Déchiffrer les code moteur toyota
vince3004 a répondu à un(e) sujet de vince3004 dans Moteur/Transmission/Entretien. de .::Club TRD Quebec::.
Oui, la différence entre GE et FE C'est la tête, a la base c'était les angle des valve, les angle des tête GE était adapté a la performance. Les FE avait des angle qui favorisais l'économie d'essence. Maintenant avec la technologie, les tête GE on perdu leur raison d'exister, car maintenant, les manifacturier peuvent concevoir des moteur économique et performant Donc l'appelation F a survécu au changement technologique. -
Choix de moteur pour célica et mr2 mkII
vince3004 a répondu à un(e) sujet de vince3004 dans Moteur/Transmission/Entretien. de .::Club TRD Quebec::.
-
Intercooling System
vince3004 a répondu à un(e) sujet de vince3004 dans Induction Forcée. de .::Club TRD Quebec::.
The Water Plumbing: The most obvious place for the pump to be within the system is immediately after the radiator, so that it is then subjected only to relatively cool water temperatures. However, this can't always be done because some designs of pump are reluctant to suck through the restriction posed by the radiator. Depending on the design of the radiator, its flow restriction may be substantial. During the assembly of the system it is therefore wise to set it all up on the bench. Check water flows with the pump running (at different speeds, if this is the approach to be taken) and with the pump in different positions within the system. The pump position that yields the greatest water flow should be the one adopted - even if that places the pump immediately after the heat exchanger. In practice, the temperature of the water exiting the heat exchanger will not be extremely high if the water volume circulating through the system is adequate. A header tank should be positioned at the highest point of the system. This should incorporate a filler cap and can actually be part of the heat exchanger if required. Note that a water/air system can be pressurised if required by the use of a radiator-type sealing cap. Be careful that the system design allows air to be bled from any spots where it will become trapped. Air in the system degrades performance and can cause pump problems. A filter placed in front of the pump is a good idea and very cheap water filters can be found in the garden irrigation section of hardware stores. These filters use a fine plastic mesh design and can be easily placed in-line. Selecting an Intercooling System: Both air/air and water/air systems have their own benefits and disadvantages. Air/air systems are generally lighter than water/air, especially when the mass of the water (1kg a litre!) is taken into account. An air/air system is less complex and if something does go wrong (the intercooler develops a leak for example), the engine behaviour will normally change noticeably. This is not the case with water/air, where if a water hose springs a leak or the pump ceases to work it will not be immediately obvious. However, an air/air intercooler uses much longer ducting and it can be very difficult to package a bulky air/air core at the front of the car - and get the ducts to it! Finally, an air/air intercooler is normally cheaper than a water/air system. A water/air intercooler is very suitable where the engine bay is tight. Getting a couple of flexible water hoses to a front radiator is easy and the heat exchanger core can be made quite compact. A water/air system is very suitable for a road car, with the thermal mass of the water meaning that temperature spikes are absorbed with ease. However, note that if driven hard and then parked, the water within the system will normally become quite warm through underbonnet heat soak. This results in high intake air temperatures after the car is re-started as the hot water takes some time to cool down. Advantages/Disadvantages: Type of Intercooling: Air/Air Advantage: * Efficient * Cheap * Japanese import cores readily available Disadvantages: * Longer induction air path * Packaging of large intercoolers difficult * Large pipes to and from intercooler required Water/Air Advantage: * Short induction air path * Easy to package * Excellent for short power bursts (ie typical road use) Disadvantages: * Heavier * More complex * More expensive * Heat exchangers harder to source -
Intercooling System
vince3004 a répondu à un(e) sujet de vince3004 dans Induction Forcée. de .::Club TRD Quebec::.
Water/Air Intercooling - Everyone always talks about air/air intercoolers. So what are the pros and cons of water/air designs? Water/air intercooling is used less frequently than the air/air approach. However, it has several benefits, especially in cramped engine bays. A water/air intercooler uses a compact heat exchanger located under the bonnet and normally placed in-line with the compressor-to-throttle body path. The heat is transferred to water which is then pumped through a dedicated front-mounted radiator cooled by the airflow generated by the car's movement. A water/air intercooler system consists of these major parts: the heat exchanger, radiator, pump, control system, and plumbing. Technically, a water/air intercooler has some distinct cooling advantages on road cars. Water has a much higher specific heat value than air. The 'specific heat value' figure shows how much energy a substance can absorb for each degree temp it rises by. A substance good at absorbing energy has a high specific heat value, while one that gets hot quickly has a low specific heat. Something with a high specific heat value can obviously absorb (and then later get rid of) lots of energy - good for cooling down the air. Air has a specific heat value of 1.01 (at a constant pressure), while the figure for water is 4.18. In other words, for each increase in temp by one degree, the same mass of water can absorb some four times more energy than air. Or, there can be vastly less flow of water than air to get the same job done. Incidentally, note that pure water is best - its specific heat value is actually degraded by 6 per cent when 23 per cent anti-freeze is added! Other commonly available fluids don't even come close to water's specific heat value. The high specific heat value of water has a real advantage in its heat sinking affect. An air/water heat exchanger designed so that it has a reasonable volume of water within it can absorb a great deal of heat during a boost spike. Even before the water pump has a chance to transfer in cool water, the heat exchanger has absorbed considerable heat from the intake airstream. It's this characteristic that makes a water/air intercooling system as efficient in normal urban driving with the pump stopped as it is with it running! To explain, the water in the heat exchanger absorbs the heat from the boosted air, feeding it back into the airstream once the car is off boost and the intake air is cooler. I am not suggesting that you don't worry about fitting a water pump, but it is a reminder that in normal driving the intercooler works in a quite different way to how it needs to perform during sustained full throttle. However, the downside of this is once the water in the system has got hot (for example, after you've been driving and then parked for a while), it takes some time for the water to cool down once you again drive off. The Heat Exchanger: Off the shelf water/air heat exchangers are much rarer than air/air types. Water/air intercooling has been used in cars produced by Lotus, Subaru and Toyota. A few aftermarket manufacturers also produce them. If you want to make your own, the easiest way to go about it is to jacket an air/air core. Pick an air/air intercooler that uses a fairly compact core that still flows well. If it uses cast alloy end tanks (as opposed to pressed sheet aluminium) then so much the better. (Plastic end tank types need not apply!) The core is then enclosed in 3mm aluminium sheet, TIG welded into place. Water attachment points can be made by welding alloy blocks to the sheet metal, with these blocks then drilled and tapped to take barbed hose fittings. Pressure-test the water jacket to make sure that it actually does seal, and make sure that the water flow from one hose fitting to the other can't bypass the core. Small baffles can be used to ensure that the water does fully circulate before exiting. Another type of water/air heat exchanger can be made using a copper tube stack. These small heat exchangers are normally used to cool boat engine oil, exchanging the heat with engine coolant or river or seawater. While the complete unit uses a cast iron enclosure and so is too heavy and large for car applications, the core piece itself can be enclosed to make a very efficient heat exchanger. Comprising a whole series of small-bore copper tubes joining two endplates, the core is cylindrical in shape and relatively easy to package. The induction air flows through the tubes while a water-tight sheet metal jacket can be soldered around the cylinder. The resulting heat exchanger is a little like a steam engine boiler, with induction air instead of fire passing down the boiler tubes! The one here is shown installed on a car undergoing fuel pump testing. As with air/air designs, the more efficient that you can make the heat exchanger, the better is the potential system performance. If you plan to use an off-the-shelf heat exchanger that has specifications available for it, you will be interested to know that the 150kW turbo Subaru Liberty (Legacy) RS uses a factory-fitted water/air exchanger that has a 4kW capacity. This heat exchanger also works quite effectively when power is increased to about 210kW. Remember in your design considerations that you want a reasonable store of water in the actual heat exchanger (2 or 3 litres at least) to help absorb the temperature spikes. Radiator and Pump The front-mounted radiator for the water/air intercooler should be completely separate to the engine cooling radiator. Some turbo trucks use the engine coolant to cool the water/air ntercooler, but their efficiency is much reduced by taking this approach. Suitable radiators that can be used include large oil coolers, car air conditioning condenser cores, and scrap domestic air conditioning condensers. If you use a car airconditioning condenser there is likely to be available a small dedicated electric fan that attaches to the core easily. This fan can be triggered to aid cooling when the vehicle is stationary. The radiator should at least match (and preferably) exceed the cooling capacity of the heat exchanger, but again finding proper specifications is often difficult. The Subaru Liberty (Legacy) RS with the 4kW heat exchanger uses quite a small radiator, only 45 x 35 x 3cm. An electric pump is the simplest way of circulating the water, with the type of pump chosen influenced by how the pump is to be operated. Some factory systems have the pump running at low speed continuously, switching to high speed at certain combinations of throttle position and engine airflow. If you follow a similar approach, the pump that is chosen must be capable of continuous operation. Another approach is to trigger the pump only when on boost, or to trigger a timing circuit that keeps the pump running for another (say) 30 seconds after the engine is off-boost. The latter type of operation will mean that the pump operating time is drastically reduced over continuous running. Twelve volt water pumps fall into two basic types - impeller and diaphragm. An impeller pump is of the low pressure, high flow type. In operation it is quiet with low vibration levels. A diaphragm pump can develop much higher pressures but generally with lower flows. A diaphragm pump is noisy and must be rubber-mounted in a car. Suitable impeller type pumps are used in boats as bilge pumps and for deck washing. They are relatively cheap and have very high flows - 30 litres a minute is common. However, they are not designed for continuous operation and generally don't have service kits available for the repair of any worn out parts. Diaphragm pumps are used to spray agricultural chemicals and to supply the pressurised water for use in boat and caravan showers and sinks. They are available in very durable designs suitable for continuous running and have repair kits available. Flows of up to 20 litres a minute are common and they develop enough pressure (45 psi) to push the water through the front mounted radiator and heat exchanger without any problems. The factory water/air intercooler system in the Subaru Liberty RS uses an impeller-type pump rated at 15 litres a minute (all flow figures are open-flow). It is automatically switched from low to high speed as required. This is an ideal pump because it was designed by Subaru to circulate the water in a water/air intercooling system! However, it is a very expensive to buy new, but if one can be sourced secondhand it is ideal. A cheap and simple impeller pump is the Whale GP99 electric pump. It is so small that the in-line pump can be supported by the hoses that connect to it. It flows 11 litres a minute and has 12mm hose fittings. It is 136 x 36mm in size and is suitable for discontinuous operation. This pump is available from marine and caravan suppliers. The Flojet 4100-143 4000 is a diaphragm pump suitable for water/air intercooler use. The US-manufactured pump uses a permanent magnet brush-type fan-cooled motor with ball-bearings and is fully rebuildable. The pumping head uses four diaphragms which are flexed by a wobble plate attached to the motor's shaft. The 19 litre/minute pump uses ¾ inch fittings and is 230mm long and 86mm in diameter. It is available from companies supplying agricultural spray equipment. The Flojet pump needs to be mounted either vertically with the pump head at the bottom, or horizontally with the vent slots in the head facing downwards. This is to stop any fluid draining into the motor if there are any sealing problems in the pump head. At its peak pressure of 280 kPa (40 psi), the pump can draw up to 14 amps; however, in intercooler operation the pressure is vastly less and so the pump draws only about 5.5 amps at 12 volts. The pump is noisy (as all diaphragm pumps are) but mounting it on a rubber gearbox crossmember mount effectively quietens it. Note that these pumps are much louder when mounted to the car's bodywork than they are when sitting on the bench! Control Systems As already indicated, there are a number of ways of controlling the pump operation. The simplest is to switch the pump on and off with a boost pressure switch. This means that whenever there is positive manifold pressure, the pump circulates the water from the heat exchanger through the radiator and back to the heat exchanger. If boost is used frequently and for only short periods, this approach works well. However, it is better if a timer circuit is used so that the pump continues to operate for a short period after boost is finished. A suitable pressure switch is an adjustable Hobbs unit (pictured), available from auto instrument suppliers. However, this switch is relatively expensive and a cheaper unit is easily found. Spa bath suppliers stock a pressure-operated switch that is ideal for forced aspirated car use. The pressure switch is designed to work as part of the air-actuated switching system which is used in a spa bath so that bathers don't have to directly operate high voltage switches. The switch triggers at around 1 psi and costs about half that of a traditional automotive pressure switch. If a switching pressure above 1 psi is required, simply tee a variable bleed into the pressure line leading to the switch. Adjusting the amount of bleed will change the switch-on point. Another approach to triggering pump operation is to use a throttle switch. A micro switch (available cheaply from electronics stores) can be used to turn on the pump whenever a throttle position over (say) half is reached. A cam can be cut from aluminium sheet and attached to the end of the throttle shaft. If shaped with care, it will turn on the switch gently and then keep it switched on at throttle positions greater than the switch-on opening throttle angle. If a two-speed pump operation is required, the pump can be fed current through a dropping resistor to provide the slow speed. When full speed is required, the dropping resistor can be bypassed. Suitable dropping resistors are the ballast resistors used in older ignition systems or the resistor pack used in series with some injectors. The value of the resistor that is used will depend on the pump current and its other operating characteristics. In all cases, the resistor will need to dissipate quite a lot of power and so will need to be of the high wattage, ceramic type. The resistor will get very hot and can be placed on a transistor-type heat sink mounted within the airstream, perhaps behind the grille. When experimenting with resistors and a pump, you should know that placing the multiple resistors in parallel will increase pump speed while wiring the resistors in series will slow the pump. Another approach is to use a temperature switch, so that the pump doesn't run when the intake air is not actually hot. This situation can occur on boost if the intake air temperature is very low because the day is cold. Overly cold intake air can cause atomisation problems, although this is not normally a problem in a high performance car being driven hard! However, running the pump when the intake air is perhaps only 5 is pointless and it can be avoided by placing a normally-open temperature switch in series with the boost pressure or throttle position switches. If the switch closes at temperatures above (say) 30 degrees, the pump will operate only when it actually needs to. A range of low cost temperature switches is available from RS Components (stores world-wide). Note that in all pump control systems a relay should be used to operate the pump Suite prochain post -
Intercooling System
vince3004 a répondu à un(e) sujet de vince3004 dans Induction Forcée. de .::Club TRD Quebec::.
Sourcing the Core There are a number of ways of getting together a very good air/air intercooler. Those companies specialising in the production of intercoolers (Spearco in the US is one of the largest) have a huge variety of cores and end-tanks available. However, as an aluminium item of fairly intricate construction, they are not cheap. For a really big air/air intercooler complete with end tanks, expect to pay about as much as you would for a turbo. An alternative in Australia are the Japanese importing wreckers. While few factory turbo cars have really large intercoolers (and even less factory supercharged cars have them!), there are at least a couple of large ones available. As mentioned previously, the Nissan Skyline GT-R and Mitsubishi Evolution model Lancers all have very good intercoolers. The Nissan Pulsar GTiR also has a large intercooler (pictured), while the Mazda RX7 single turbo Series 4 has an engine-mounted intercooler that has a good flow, despite its appearance. Welding two of the RX7 intercoolers in series has also been shown to work very well. You can also produce your own intercooler by modifying heat exchanger cores designed for other duties. However, having personally done so, I can advise that it is a great deal of work! One source of efficient heat exchangers are old airconditioners. Domestic and industrial refrigerative airconditioners use copper tube and aluminium fin heat exchangers for both their evaporators and condensers. When the airconditioner is discarded (perhaps because of a faulty compressor) these components are sold off at scrap value - less than the price of a few spark plugs! If you are patient and handy, you can cut off each end of the core and make plates that fit over the multiple copper tubes. Making end tanks that attach to these baseplates is then straightforward. The resulting copper-cored air/air intercooler is efficient and very, very cheap. Another alternative it is to visit truck wreckers. Diesel turbo truck intercoolers are absolutely huge. They can also often be picked up very cheaply from insurance repair jobs, where the core has been twisted slightly, or one end tank damaged perhaps. If you chose with an eye to modification, the core will be able to be shortened without new end tanks being required - which substantially reduces the amount of work! This way you need only make new blanking plates for the ends of the shortened tanks. However, be aware that reducing the number of tubes of a truck intercooler in this manner can also reduce its flow by an unacceptable amount. -
Intercooling System
vince3004 a répondu à un(e) sujet de vince3004 dans Induction Forcée. de .::Club TRD Quebec::.
Intercooler Mounting When either increasing the size of a factory intercooler or installing a new one for a custom forced aspirated car, care needs to be given to the location that is chosen. The first point to consider is the amount of ambient heat that is present. An intercooler core absorbs heat just as well as it sheds it. This means that an underbonnet intercooler core can easily become an intake air pre-heater if care isn't taken with its location. Turbo cars run especially high underbonnet temps and so a bonnet vent designed for intercooler cooling while the car is under way can easily become a "chimney" ducting out hot air while the car is stationery - hot air that passes straight through the intercooler core. In fact, the behaviour of the intercooler while the vehicle is stopped is very important if you're in the habit of caning the car in traffic light Grands Prix! By far the best location for an intercooler is in front of the engine radiator. The car manufacturer will have aerodynamically tested the vehicle to ensure that large volumes of air pass through the engine cooling radiator, and so an intercooler placed in front of that is sure to receive a great amount of cooling air. Note that the intercooler should be in front of any air conditioning condenser as well! The air/air core should be ducted with the cold air if at all possible. Many people simply place the intercooler at the front of the car, hoping that the air being forced through the front grille will all pass through the intercooler. However, if there is an easier path for the air to take, that's the way it will go. Sheet metal guides can be used to channel the air coming in the grille through the intercooler, and foam rubber strips can be used to seal the escape routes that the air might otherwise take. The plumbing leading to and from the intercooler should produce only a minimal pressure drop. Factory turbo cars often use intake ducts that smoothly increase in size from the diameter of the turbo compressor outlet (often only 50mm or so) to the inlet diameter of the throttle body (perhaps 80mm) and if this can be done, it's an approach which should be followed. Intercooler plumbing should have gentle curves and be as short as possible. Don't forget when you are planning the plumbing that the engine (and so also the blower or turbo!) moves around, while the body-mounted intercooler core does not. This means that some rubber or silicone hose connections must to be incorporated in the plumbing to absorb the movement. The return duct from the intercooler should be insulated to avoid it picking up heat from within the engine bay. Lagging the pipe with fibreglass or ceramic fibre matting works effectively without being too bulky. The pipework can be finished off with a wrapping of aluminium adhesive tape of the type sometimes used to seal roofs. Also note when planning the intercooler pipework that the compressor cover of a turbo can be easily rotated to allow the outlet to come out at a different angle. This can reduce the number and tightness of the bends required. Some people believe that if they fit a very big intercooler with large ducts, the volume of charge air within it will unduly slow throttle response. Their concern is unjustified however - throttle response problems (for example, turbo lag) are largely the result of other factors within the forced induction system, not the volume of air within it. -
Intercooling System
vince3004 a répondu à un(e) sujet de vince3004 dans Induction Forcée. de .::Club TRD Quebec::.
Intercooler Efficiency An intercooler will do two things - it will lower the temperature of the intake air and at the same time, cause a slight drop in boost pressure. The latter comes from the restriction to flow caused by the intercooler. Some restriction is unavoidable because the flow through an efficient intercooler core needs to be turbulent if a lot of the air is to come in contact with the heat exchanger surfaces. However, if the pressure drop is too high, power will suffer. A pressure drop of 1-2 psi can be considered acceptable if it is accompanied by good intercooler efficiency. Intercooler efficiency is a measurement of how effective the intercooler is at reducing the inlet air temperature. If the intercooler reduces the temperature of the air exiting the compressor to ambient, the intercooler will be 100 per cent efficient. It will also be a bloody marvel, because no conventional intercooler can actually achieve this! Typical figures for a good intercooler are around 70 per cent. Intercooler Types: Most intercoolers fall into two categories - air/air and air/water. There are also those special designs that cool the intake air to below ambient temperatures, using ice, the air-conditioning system or direct nitrous oxide sprays, but they will not be covered here. Air/Air Intercoolers: Air/air intercoolers are the most common type, both in factory forced induction cars and aftermarket. They are technically simple, rugged and reliable. An air/air intercooler consists of a tube and fin radiator. The induction air passes through thin rectangular cross-section tubes that are stacked on top of the other. Often inside the tubes are fins that are designed to create turbulence and so improve heat exchange. Between the tubes are more fins, usually bent in a zig-zag formation. Invariably, air/air intercoolers are constructed from aluminium. The induction air flows through the many tubes. The air is then exposed to a very large surface area of conductive aluminium that absorbs and transfers the heat through the thickness of metal. Outside air - driven through the core by the forward motion of the car - takes this heat away, transferring it from the intake air to the atmosphere. Described above is what is normally called the intercooler 'core' - the part of the intercooler that actually effects the heat transfer. However, there also needs to be an efficient way of carrying the intake air to each of the tiny tubes that pass through the core. End-tanks are used for this, being welded at each end of the core. While some cores are 'double-pass' (the inlet and outlet tanks are at one end separated by a divider, while at the other end the air does a U-turn), most cores are single-pass, with the inlet at one end of the core and the outlet at the other. Good intercooler manufacturers have two specifications available - the pressure drop at a rated airflow (with the airflow often expressed as engine power), and the cooling effect (normally expressed as a temperature drop at that rated flow). However, many intercooler manufacturers have no data available on either of these factors! To some extent this doesn't matter greatly - the design of the intercooler is normally limited by factors other than heat transfer ability and pressure drop. Because an air/air intercooler uses ambient air as the cooling medium, an air/air intercooler cannot be too efficient - simply, the bigger the intercooler, the better. In fact, the maximum size of an air/air intercooler is normally dictated by the amount of space available at the front of the car and the size of your wallet, rather than any other factors! It's easy to see how cost is a vital factor - those forced induction cars produced by major car companies as homologation specials (either for rallying or circuit racing) have quite huge intercoolers that dwarf the ones fitted by the same companies to their humdrum cars. Nissan used an air/air core no less than 60 x 30 x 6cm on their R32 Nissan Skyline GT-R and the Mitsubishi Lancer Evolution vehicles also use huge intercoolers. The "bigger is better" philosophy can be clearly seen at work in these cars. Many factory-fitted intercoolers are undersized. Air/air cores no larger than a paperback book can be found in turbo cars with a nominal maximum output of 150kW. Cars equipped with this type of intercooler can be held at peak power for only a very short time before the increasing inlet air temperature causes the ECU to retard timing or decrease boost. A car fitted with this type of tiny factory intercooler is almost impossible to dyno test - the intake air temp rises so fast that rarely can more than one consecutive dyno run be made before the intake air temp is so high that the engine detonates... On the other hand, the aforesaid Skyline GT-R has a measured intake temp of 45C on a 35C day at 1 Bar boost and a sustained full-throttle 250 km/h! -
The Complete Guide to Intercooling If you run a turbo or blown car, you need an intercooler for best performance. By Julian Edgar When a turbo or supercharger compresses air, the air is heated up. While this hot air can be fed straight into the intake of the engine (and often is), there are two disadvantages in taking this approach. Firstly, warm air has less density than cool air - this means that it weighs less. It's important to know that it's the mass of air breathed by the engine that determines power, not the volume. So if the engine is being fed warm, high pressure air, the maximum power possible is significantly lower than if it is inhaling cold, high pressure air. The second problem with an engine breathing warm air is that the likelihood of detonation is increased. Detonation is a process of unstable combustion, where the flame front does not move progressively through the combustion chamber. Instead, the air/fuel mixture explodes into action. When this occurs, damage to the pistons, rings or head can very quickly happen. If the temperature of the air can be reduced following the turbo or supercharger, the engine will have the potential to safely develop a higher power output. Intercoolers are used to cause this temperature drop. Temperature Increase: There are a number of factors that affect the temperature increase that occurs when the air is compressed. Firstly, the higher the boost pressure, the greater will be the temperature increase. As a rule of thumb, if you are using a boost pressure level of more than about 0.5 Bar (~ 7 psi), an intercooler is generally a worthwhile investment. Secondly, the lower the efficiency of the compressor, the higher the outlet air temp. However, it is difficult to accurately estimate the efficiency of the compressor and even if such a figure is available, it doesn't necessarily apply to all the different airflows that the compressor is capable of producing. In other words, there will be some combinations of airflow and boost pressure where the compressor is working at peak efficiency - and other areas where it isn't. While a well-matched compressor should be at peak efficiency most of the time, in some situations it will be working at less than optimum efficiency. This will change the outlet air temperature, usually for the worse. Thirdly, the turbo- or supercharged car engine is not working in steady-state conditions. A typical forced induction road car might be on boost for only 5 per cent of the time, and even when it is on boost, it is perhaps for only 20 seconds at a stretch. Any decent forced induction road car will be travelling at well over 160 km/h if given 20 seconds of full boost from a standstill, meaning that longer periods of high boost occur only when hill-climbing, towing or driving at maximum speed. While all of the engine systems should be designed with the maximum full load capability in mind, in reality very few cars will ever experience this. This factor means that the heat-sink ability of the intake system must be considered. If the inlet air temperature of the engine in cruise condition is 20°C above ambient, then on a 25° day the inlet air temp will be 45°C. After 30 minutes or so of running, all of the different components of the intake system will also have stabilised at around this temperature. If the engine then comes on boost and there is a sudden rise in the temp of the air being introduced to this system, the temperature of the turbo compressor cover (or blower housing), inlet duct, throttle body, plenum chamber, and inlet runners will all increase. These components increase in temp because they are removing heat from the intake air, limiting the magnitude of the initial rise in the actual intake air temperature. As a result, the infrequent short bursts of boost used in a typical road-driven forced-induction car often produce a lower initial intake air temperature than expected. This doesn't mean that intercooling is not worthwhile - it certainly is - but that the theory of the temperature increase doesn't always match reality.